Foil Bearings - Technology Whose Time Has Come - Part 1
By Peter Chapman
This first part of a two-part post gives an excellent introduction to what foil bearings are, and why they are an excellent choice in certain situations. Part 2 reviews foil bearing development history, the technical sweet spot for use, and why this is indeed a technology whose time has come.
What is a Foil Bearing?
A foil bearing is a hydrodynamic bearing; that is, the pressure profile within the bearing that supports the shaft is generated by the relative motion between the rotating shaft and the stationary foils. It uses the surrounding fluid (often air or another gas, but can be liquid or mixed-phase) instead of a traditional lubricant, such as oil or grease. The bearing is made up of multiple layers of foils, usually consisting of a smooth top foil supported by an underlayment of corrugated or bump foils. It is the compliance of the underlying foils that gives a foil bearing its characteristic performance.
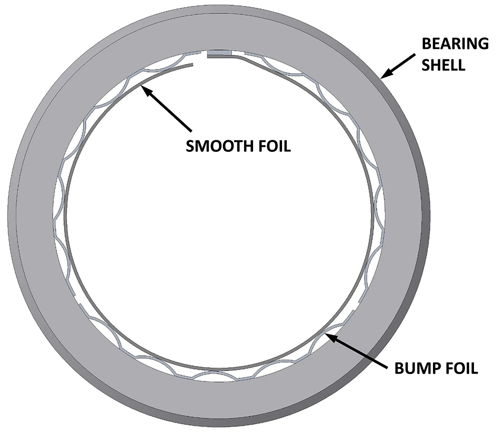
Why Use Foil Bearings?
Foil bearings offer many benefits that make them attractive for some of today’s advanced machine designs. The primary advantages of foil bearings are:
- Ability to operate at very high speeds (in excess of 100,000 rpm)
- Operate without the need for oil or grease lubrication
- Near-infinite service life eliminates the need for frequent maintenance intervals
- Simple, compact designs offer reduced system cost
High-Speed Operation
Foil bearings far exceed the speed limitations of current rolling element bearings. A bearing’s dN value (the product of the bearing diameter in mm and the running speed) is used to rate and compare its speed capacity to other bearings. The following chart shows a comparison of the dN limits for different bearing systems. At present, it is not known if there is a dN limit for foil bearings.
In oil-lubricated bearings, power losses increase exponentially as the flow within the bearing transitions from laminar to turbulent flow. Higher power loss results in lower system efficiency, as well as higher flow rates to keep the bearings cool. This in turn requires more power, and efficiency suffers even further.
Oil- and Grease-Free Operation
For many systems, oil or grease used for bearings is a source of contamination. Infiltration of oil into the process fluid can negatively impact the performance, and in cases where purity of the process fluid is critical, their use may be outright prohibited. Eliminating the lubrication system also results in a simpler, more cost-effective system by eliminating the need for ancillary equipment (and related maintenance), such as pumps, coolers, filters, and seals.
Wide Temperature Capability
Because oils and greases start to break down as temperature increases, their use is limited to applications around 300°F/150°C. Foil bearings are capable of surviving significantly higher temperatures, with some protective coatings being able to withstand 1200°-1400°F/650°-760°C. On the opposite end of the scale, foil bearings are immune to extreme cold, down to cryogenic temperatures, while liquid lubricants become too viscous for effective use at these temperatures.
Want to Learn More?
Keep reading with Part 2 to learn more about the history of foil bearing development, and the technical and markets factors that make this a technology to watch and consider. If you’d like to speak with an experienced foil bearing design engineer about your system requirements and if this technology makes sense for your application, contact us.